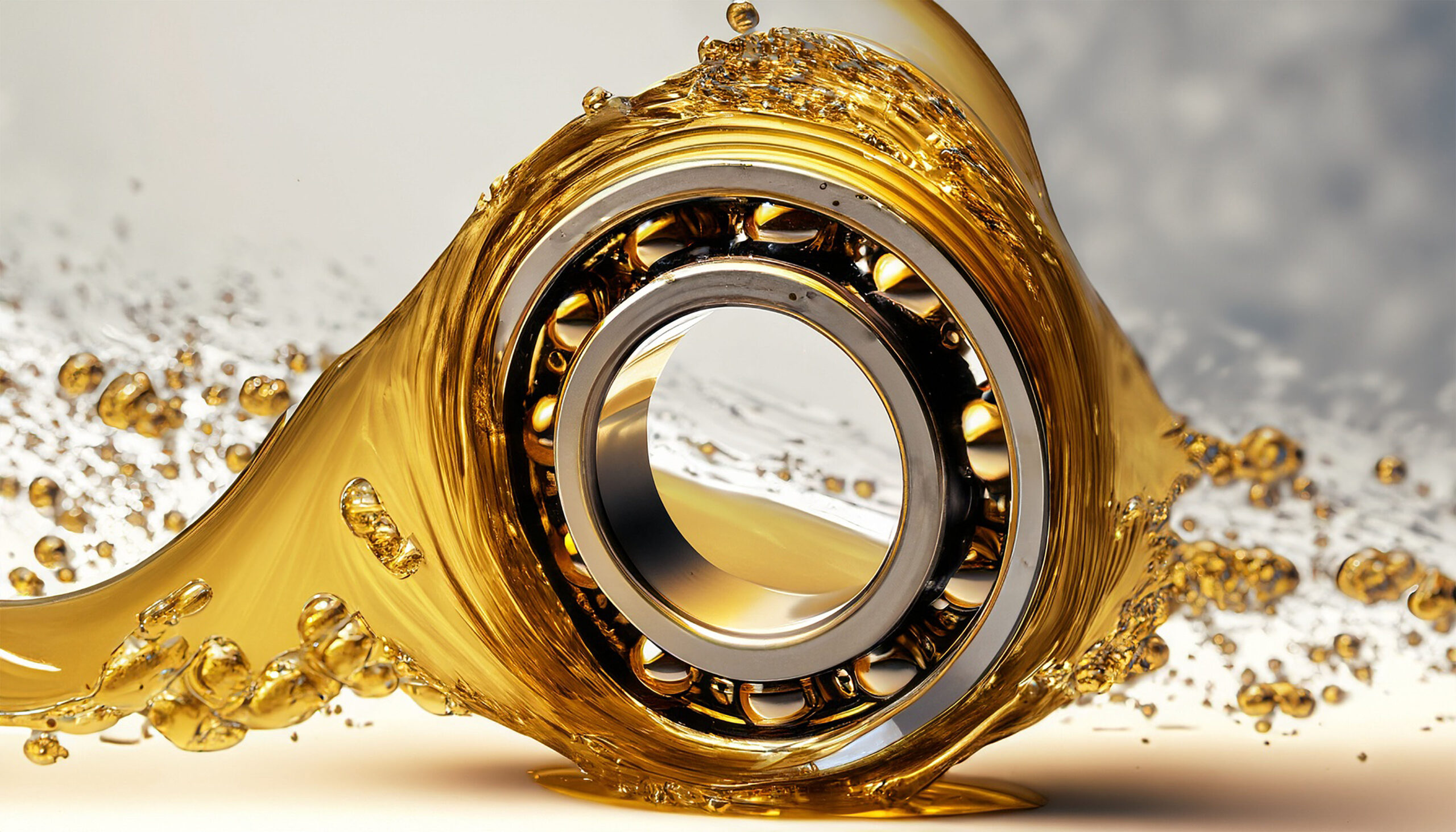
Understanding the Critical Role of Bearings in Power Plants
Bearings are a critical component of power plants, enabling smooth and efficient functioning of essential machinery. From turbines to electric motors and pumps, these vital components reduce friction and ensure reliable operation. Yet, bearing failure is a common and costly issue faced by engineers. Addressing this challenge requires proactive maintenance, proper troubleshooting, and access to expert services such as those provided by Fusion Babbitting. With decades of expertise in Babbitt bearing services, Fusion Babbitting has become a trusted partner for power plant engineers nationwide.
Common Causes of Bearing Failure in Power Plants
Bearing failure can bring operations in a power plant to a standstill, leading to unplanned downtime, expensive repairs, and potential safety risks. Understanding the root causes of failure is the first step toward prevention. Let’s examine some key factors.
1. Insufficient Lubrication
Lubrication plays a crucial role in preventing bearing wear and tear. However, insufficient or improper lubrication can lead to overheating, increased friction, and eventual bearing failure. Regular checks of lubrication levels and using the correct lubricant for specific applications can mitigate this risk.
2. Contamination
Contaminants such as dirt, moisture, and debris can infiltrate bearing systems, leading to corrosion and accelerated damage. Effective sealing systems and routine cleaning can help keep bearings in good condition.
3. Overloading and Misalignment
Bearings in power plants often carry heavy loads. Excessive load or misalignment can cause uneven wear and lead to premature bearing failure. Ensuring proper alignment and using bearings designed for specific load requirements can alleviate this issue.
4. Fatigue and Wear
Bearings experience immense pressure during prolonged operations, especially in power plant machinery. Over time, fatigue cracks and surface wear can occur, reducing bearing longevity. Predictive maintenance schedules can detect early signs of wear and help prolong the life of vital components.
Warning Signs of Bearing Failure
Early detection of bearing issues can save power plants from costly repairs and extended downtime. Faulty bearings often exhibit specific warning signs. Engineers and maintenance teams should remain vigilant for the following indicators:
1. Unusual Noise
Grinding, squealing, or rumbling sounds are often the first indication of a problem. Such noises suggest misalignment, insufficient lubrication, or internal damage to the bearing.
2. Overheating
Excess heat may indicate friction within the bearing, often caused by improper lubrication or overloading. Monitoring operating temperatures can provide an early warning of potential failures.
3. Vibration
Excessive vibration in machinery is another major red flag. Vibrations can result from wear, damage, or imbalance in the bearing system. Predictive maintenance tools can help identify vibration anomalies before they escalate.
4. Decreased Performance
A noticeable drop in machine efficiency or performance could signal issues with internal components, including bearings. Regular inspections can help pinpoint the source of inefficiencies.
Best Practices for Preventing Bearing Failure
Preventing bearing failure in power plants requires a combination of proactive maintenance, advanced diagnostic techniques, and high-quality repairs. Here are some essential strategies to keep bearings operating effectively:
1. Routine Inspections and Monitoring
Routine inspections are key to identifying potential bearing issues in their early stages. Use tools such as infrared thermography, vibration analysis, and ultrasonic monitoring to detect problems before they escalate. Regular assessments can prevent small concerns from snowballing into catastrophic failures.
2. Proper Installation
Improper installation is a common cause of bearing damage. Always follow manufacturer specifications and utilize the right tools to ensure alignment and secure fittings. As experts in the field, Fusion Babbitting can offer guidance and manufacturing solutions for specialized applications, ensuring a perfect fit every time.
3. Lubrication Management
Maintaining proper lubrication is essential for maximizing bearing performance. Select lubricants that are specifically designed for high-load and high-temperature conditions common in power plants. Regularly check lubricant levels, and replace outdated or contaminated lubricants as needed.
4. Expert Repairs and Replacement
When bearings show significant wear or damage, immediate repairs or replacement are critical. With over 40 years of combined expertise, Fusion Babbitting specializes in the repair, rebabbitting, and rebuilding of industrial bearings. Their high-quality services ensure components meet or exceed OEM specifications, making them a reliable partner for power plant professionals.
The Fusion Babbitting Difference
Fusion Babbitting, based in Milwaukee, WI, has been serving industries like fossil and nuclear power plants since 1988. Specializing in Babbitt bearing services, they offer a range of solutions tailored to the needs of modern power plants. Whether it’s centrifugal casting, rebabbitting, reverse engineering, or custom manufacturing, their focus is on delivering unmatched precision and performance.
1. Comprehensive Repair Services
Fusion Babbitting provides expert repair, rebabbitting, and rebuilding services, ensuring bearings are restored to optimal condition. Their commitment to quality ensures machinery operates efficiently and minimizes downtime in critical power plant operations.
2. Reverse Engineering for Obsolete Bearings
Power plants often rely on machinery with components that are no longer in production. Fusion Babbitting’s reverse engineering capabilities allow them to create accurate replicas of obsolete bearings, complete with detailed drawings and quality materials. This innovative approach helps power plants maintain their operations without costly equipment upgrades.
3. Custom Manufacturing for High-Precision Applications
Some power plant applications require bearings specifically designed to handle unique operating conditions. Fusion Babbitting’s custom manufacturing services produce high-precision bearing products that meet even the most challenging OEM requirements.
Emergency Support When You Need It Most
Power plants operate around the clock, often making emergency support essential. Fusion Babbitting offers 24-hour emergency services to help clients nationwide. Their skilled team is equipped to handle urgent bearing repairs, reducing the impact of unexpected downtime on power plant operations. This commitment to superior service and rapid turnaround makes Fusion Babbitting a trusted name in the industry.
Conclusion: Safeguarding Power Plant Performance with Expert Maintenance
Bearings are the backbone of reliable power plant operations. By understanding common causes of bearing failure, recognizing early warning signs, and implementing preventative maintenance practices, engineers can avoid costly downtime and extend the lifespan of vital machinery. Partnering with seasoned professionals like Fusion Babbitting further ensures top-tier repair, rebuilding, and custom manufacturing services tailored to power plant needs. Their expertise in Babbitt bearing maintenance and repair sets them apart as a partner committed to operational excellence. Invest in quality maintenance today to safeguard tomorrow’s efficiency.