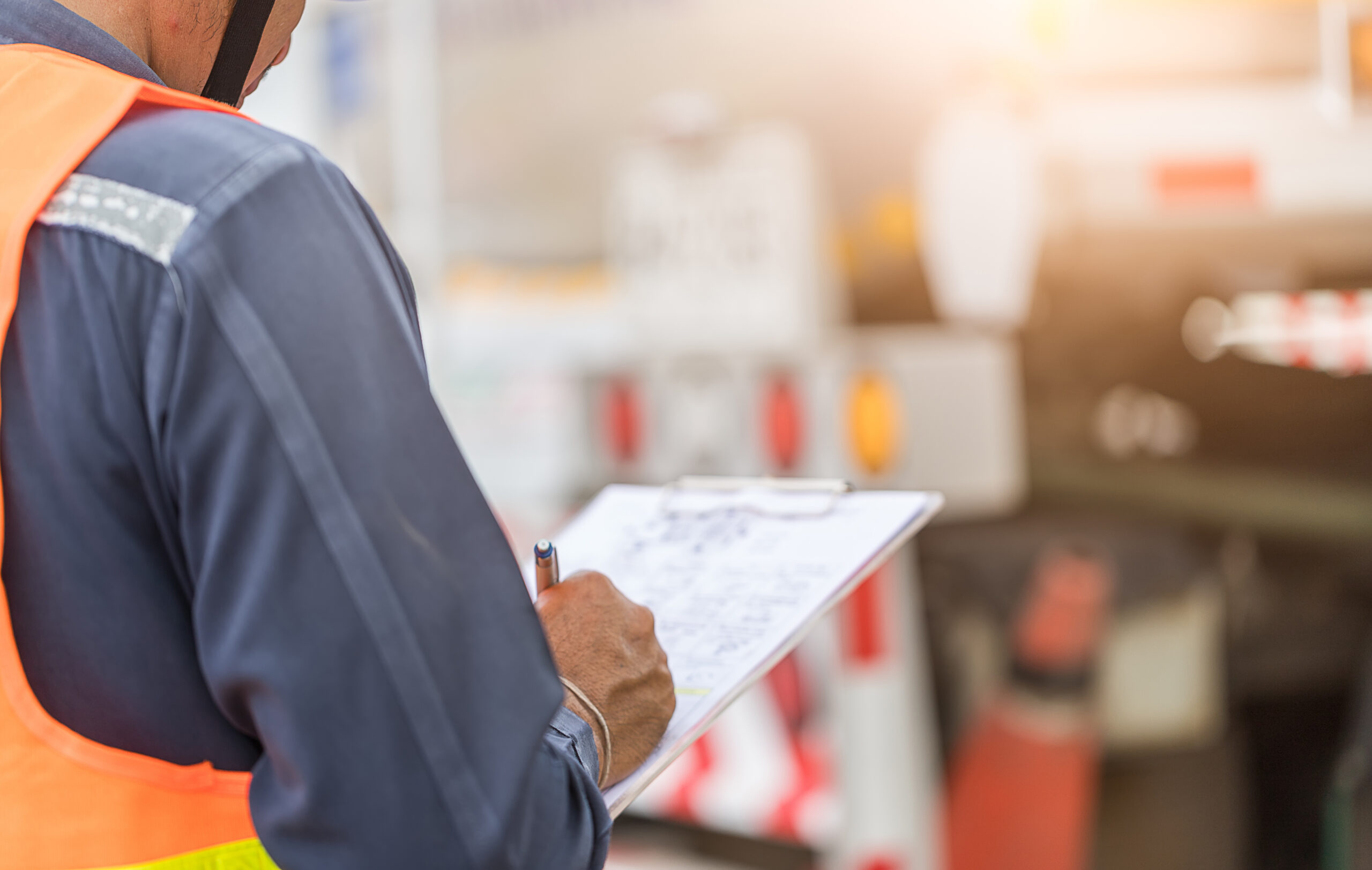
Why Bearing Inspections Are Critical Before Equipment Shutdowns
In the bustling industrial landscape of Milwaukee, WI, where the hum of motors and turbines is the soundtrack of productivity, bearing inspections might not always top the list of priorities. However, when it comes to ensuring the longevity and efficiency of your equipment, these inspections should be non-negotiable. As we head deeper into 2024, the stakes are higher than ever for maintaining seamless operations, and understanding why bearing inspections are critical before equipment shutdowns can make all the difference.
The Hidden Dangers of Skipping Bearing Inspections
Bearings play a pivotal role in the smooth operation of industrial machinery. They reduce friction, support rotational movement, and bear loads that keep the entire system running. Yet, despite their importance, bearings often go unnoticed until something goes wrong. Skipping bearing inspections before an equipment shutdown can lead to catastrophic failures, unplanned downtime, and costly repairs—none of which any business wants to face.
In 2024, with advancements in technology and stricter regulations, the importance of bearing inspections has only intensified. Companies are under pressure to maximize efficiency and minimize downtime, making proactive maintenance a key component of any successful operation. Bearing inspections are not just a routine task; they are a vital safeguard against potential disasters.
Why Timing Matters: Pre-Shutdown Inspections
You might wonder, why specifically conduct bearing inspections before a scheduled equipment shutdown? The answer lies in the opportunity to identify and address issues before they escalate. When equipment is operational, it can be challenging to detect wear and tear on bearings. However, during a shutdown, the machinery is idle, providing a perfect window to perform thorough inspections.
A pre-shutdown inspection allows technicians to assess the condition of bearings without the pressure of imminent production demands. This proactive approach can reveal early signs of damage, such as pitting, spalling, or unusual wear patterns. Addressing these issues before they become severe can prevent unexpected failures when the equipment is restarted, ensuring a smooth and trouble-free operation.
Bearing Inspection Techniques: What’s Involved?
Inspecting bearings is a meticulous process that requires specialized knowledge and tools. At Fusion Babbitting Co., we employ a range of techniques to ensure our clients’ bearings are in optimal condition. Here’s a glimpse into what’s involved in a comprehensive bearing inspection:
- Visual Inspection: Technicians look for obvious signs of damage, such as cracks, corrosion, or discoloration.
- Dimensional Inspection: Measuring the bearing’s dimensions to ensure they are within the manufacturer’s specifications.
- Non-Destructive Testing (NDT): Techniques like ultrasonic testing or magnetic particle inspection are used to detect subsurface defects.
- Lubrication Analysis: Assessing the condition of the lubricant to determine if it’s providing adequate protection.
Each of these steps is crucial in identifying potential issues that could lead to bearing failure. By catching problems early, you can avoid the costly consequences of a complete bearing breakdown.
The Cost of Neglect: Real-World Examples from 2024
To put the importance of bearing inspections into perspective, let’s look at a few real-world examples from 2024 where neglecting this critical maintenance step led to significant consequences.
- Case Study 1: Power Plant Shutdown in Milwaukee A major power plant in Milwaukee experienced an unexpected shutdown due to a bearing failure in one of its turbines. The failure resulted in a two-week outage, costing the plant millions in lost revenue and repair expenses. A pre-shutdown inspection could have identified the deteriorating bearing, preventing the catastrophic failure and the resulting downtime.
- Case Study 2: Manufacturing Plant Efficiency Loss A local manufacturing plant in Milwaukee faced a significant efficiency drop after restarting equipment post-shutdown. The cause? Worn-out bearings that were not inspected before the shutdown. The plant had to halt operations again for emergency repairs, leading to delays and increased costs. This situation could have been avoided with a simple pre-shutdown bearing inspection.
These examples highlight the potential risks of skipping bearing inspections. In both cases, a proactive approach could have saved time, money, and headaches.
2024’s Best Practices for Bearing Inspection and Repair
As we navigate through 2024, best practices in bearing inspection and repair are evolving to meet the demands of modern industries. Companies like Fusion Babbitting Co. are at the forefront of these advancements, offering cutting-edge services that ensure bearings are in top-notch condition.
Here are a few best practices to keep in mind:
- Regular Maintenance Schedule: Establish a regular maintenance schedule that includes routine bearing inspections, especially before planned shutdowns.
- Training and Expertise: Ensure your maintenance team is trained in the latest inspection techniques and understands the importance of early detection.
- Partnership with Experts: Collaborate with experts like Fusion Babbitting Co. for specialized inspection and repair services. Their experience and expertise can make a significant difference in the longevity of your equipment.
- Use of Advanced Technology: Leverage advanced technologies like condition monitoring systems to continuously assess bearing health and predict potential failures.
By following these best practices, you can stay ahead of potential issues and keep your equipment running smoothly throughout 2024 and beyond.
Safeguard Your Equipment with Fusion Babbitting Co.
In a fast-paced industrial environment like Milwaukee, WI, where every second of uptime counts, bearing inspections before equipment shutdowns are not just important—they’re essential. Don’t wait for a costly failure to remind you of their importance. Partner with Fusion Babbitting Co. today to ensure your bearings are in optimal condition and ready to handle the demands of 2024.
Our team of experts is ready to assist you with comprehensive bearing inspection and repair services tailored to your specific needs. Contact us today to schedule your next inspection and take the first step towards a more efficient and reliable operation.